First thing I can suggest is to fill in the name of the I/O with a number so you can copy this program easily to more AHU’s later on. Instead of ‘TEMPERATURE’ we can name that as AHU1 TEMPERATURE for example.
At Tab2 I have also added a short label, these 8 char names are used in the programming while the longer 20 character name at Tab1 is used only in the graphical displays.
I also notice you have a very large calibration factor at Tab3, perhaps you were experimenting with no actual sensor attached. Rather than add the large calibration factor you can put the item into manual at Tab4 and type in a new value. Just remember to put the item back into auto once you start commissioning.
Next I added a schedule and gave it a name.
And added a couple of variables, one to hold the room temp setpoint and one for the pressure setting.
Next create the PID loops, one for room temp and one for pressure control
While doing that I realized we need to set up the custom analog table for the pressure sensor on input 2. I just threw in some numbers for a ‘10inch water column’ sensor operating over 0-10V control signal. You can edit to suit your particular pressure sensor easily. Pay particular attention to the Signal type setting at Tab5, this is where you select 0-10V, 4-20ma, 0-5V or whatever type of sensor signal you have.
Then I did a very quick program, feel free to tweak and add more logic. The alarm programs will trigger an alarm when the high temp or other condition is met for 100 seconds. The progrm is running as shown at Tab6 and your other two programs further down are OFF. Programs will fight with each other so it will be best for you to delete those other two programs you had in the controller, at Tab7 they show as zeroed out now.
Two things to remember for folks new to this system:
-
You dont need a goto line at the end of the program to jump back up to the start, that is handled automatically after each run through the logic by the controller. Just let the program flow from the top line to the bottom, keep all lines for each output close together as shown and certainly dont spread logic for a given output to another program.
-
Lines further down have higher priority than the lines further up, so line 30 for the fan selector switch will override the line 20 with the schedule.
To be done: I notice the line numbers are not auto-refreshing. They’re only used for gotos which I never use myself. Still, I’ll have our developer automatically renumber programs when you hit send.
Here’s the program at this point:
AHU1Rev1.prog (64.5 KB)
To be done: Graphics. Searching this forum for graphics and you’ll see a good example or two. Source for Graphics
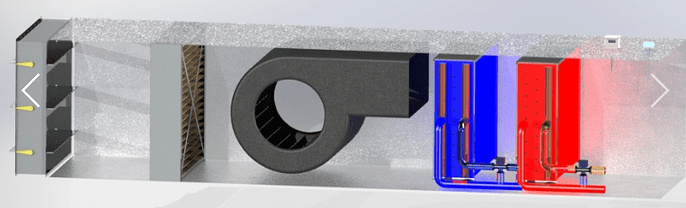