There are hundreds of thousands of systems out there running right now exactly like I described. If you were truly a mechanical engineer that has specialized in refrigeration, you would have known exactly what kind of system I am talking about.
As a matter of fact, I can name 3 “Big Brand” control systems that do exactly what I am trying to do, without having to keep pistons and connecting rods handy. But just the “controller” cost as much as one of those compressors. And it has no input or outputs. You still have to buy more hardware.
You should open your mind a little. At this point, I love the controller, but the forums are garbage if this is the attitude I am going to get. I thought this was about working to create something better, but apparently you have it all figured out.
And for what its worth, I could have said “valve” or “relay” or “light level” or any other term.
A compressor IS A pump.
Now, anyone else actually want to help or have I stumbled upon another group of closed minded people that don’t want to improve what’s offered in the market place?
I asked for help, not criticism, and on my first post to this forum, you spent 85% of your response criticizing what I am trying to do without asking questions.
THEN you asked the pertinent question, and criticized my response!
So, what good did you do? Nothing.
Now,
Let’s see what kind of response i get with this reworded…
Let’s say I am attempting to maintain a suction header pressure setpoint of 45psig on R407a, who’s SST at 45psig is 22deg F (meaning a coil temp of 22deg F), this is the lowest walk in cooler evaporator setpoint of 22deg F SST, which will give the lowest temp cooler a operating temp of 32deg F. Pretend there are 6 systems feeding back to this header. The EPR is set fully open for cooler 1, which has a setpoint of 32 deg F. Coolers 2 and 3 EPR’s are set to 25deg F SST, for a 35deg F cooler, and cooler 4 is set to 35deg F SST as a prep/cutting room of 45 deg F. Coolers 5 and 6 have an SST of 32deg F for a cooler temp of 42deg F (produce storage).
Pretend total refrigeration load for this system is 75,000btu.
I have 4 available compressors, with different capacities, that can be used to maintain the setpoint depending on what the pressure does, and how fast. (Eg, PID) If the pressure goes up, more pumps come on. pressure goes down, pumps turn off.
The compressors have the available capacity of 10%(7,500BTU), 20%(15,000BTU), 30%(22,500BTU), 40% (30,000BTU), for a total of 100% load of 75,000BTU. Meaning if everything was feeding to the suction header wide open, you would need pumps 1,2,3,4. If you were only running at a little below 50% (say 35,000BTU), you may only need pump 4. If running at 25% capacity (18,500BTU), it would only run pump 2, and occasionally bring on pump 1. If running at 60% (45,000BTU), it would only need compressor 4, and ocassionally1. The suction header pressure will fluctuate depending on load and defrost schedule.
I’d have a 2-4psig deadband (depending on how the T3000 interprets deadband. Some controllers add the “deadband setting” to each side of the setpoint, and some split the difference), so as the suction pressure creeps up or down, it would need to stage pumps on of off to stay within that deadband without bringing on too much capacity and short cycling (which I am sure the person responding to this question is worried about)
How do I turn the PID loop output into deciding what compressor(s) to start or stop based on whats already running and choosing from what’s available to start, or what’s running to stop?
If the PID calculation is raising slowly, then it would bring on a smaller compressor. If the pressure rose quickly (2 coolers were off for cleaning overnight and restarted the next morning), it would bring on a bigger compressor due to the speed of climb.
Soooo, again… Ideas? Questions?
I’ll figure it out, but I was hoping someone else already did.
Here are the different combinations of “stages” I’m trying to figure how how to choose from.
Say we are at Stage 8, and the pressure increases slowly, the control would go to stage 10. But if it increased quickly, instead of banging through the stages, it would calculate to jump to say, Stage 12. It would wait a predetermined amount of time (say 60 seconds), and check the PID against what was needed, to stage up or down, and choose depending on the speed of increase or decrease.
Will a PID output percentage go negative? I think that may be the key to the whole thing. If PID output is low, the calculation will not do anything. It works as the output goes higher. The output would have to be a negative percentage to figure a stage down, would it not?
I could be overthinking the whole thing, but that’s why I am here.
Also, To help equalize runtime, it would be nice to use even stages going up in capacity on Stages 5-10, and odd when decreasing capacity. But that’s a whole other discussion most likely.
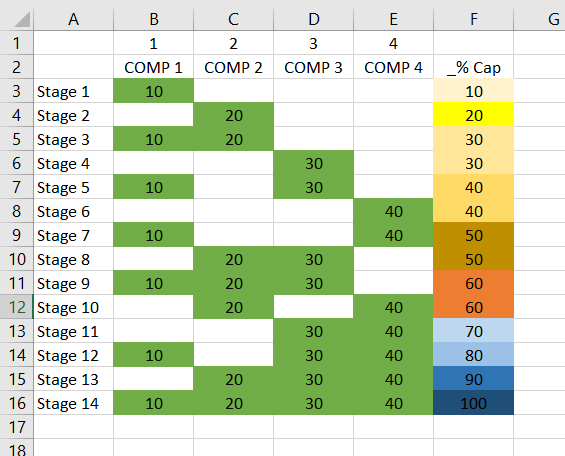